
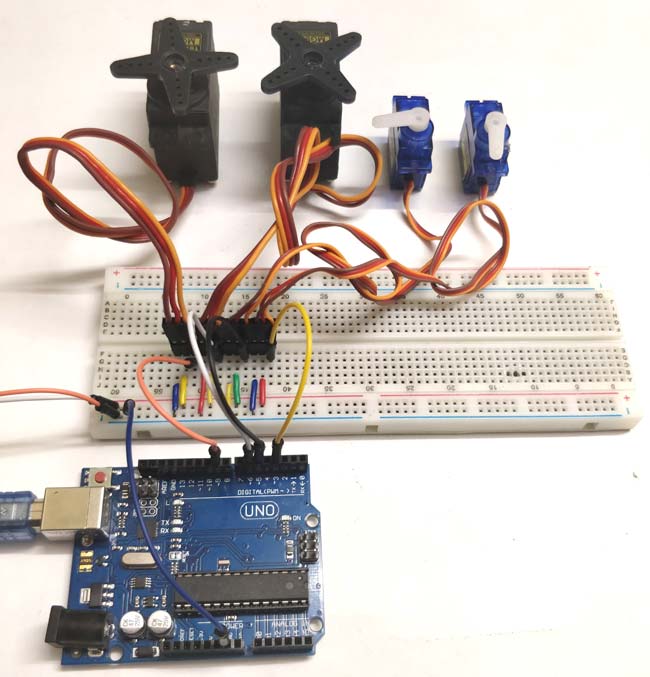
- #LARGE SERVO MOTOR ARDUINO HOW TO#
- #LARGE SERVO MOTOR ARDUINO CODE#
- #LARGE SERVO MOTOR ARDUINO FREE#
The complete Arduino code for Multiple Servo Control is given at the end.Īrduino has library for Servo Motors and it handles all the PWM related things to rotate the servo, you just need to enter the angle to which you want to rotate and there is function servo1.write(angle) which will rotate the servo to desired angle.
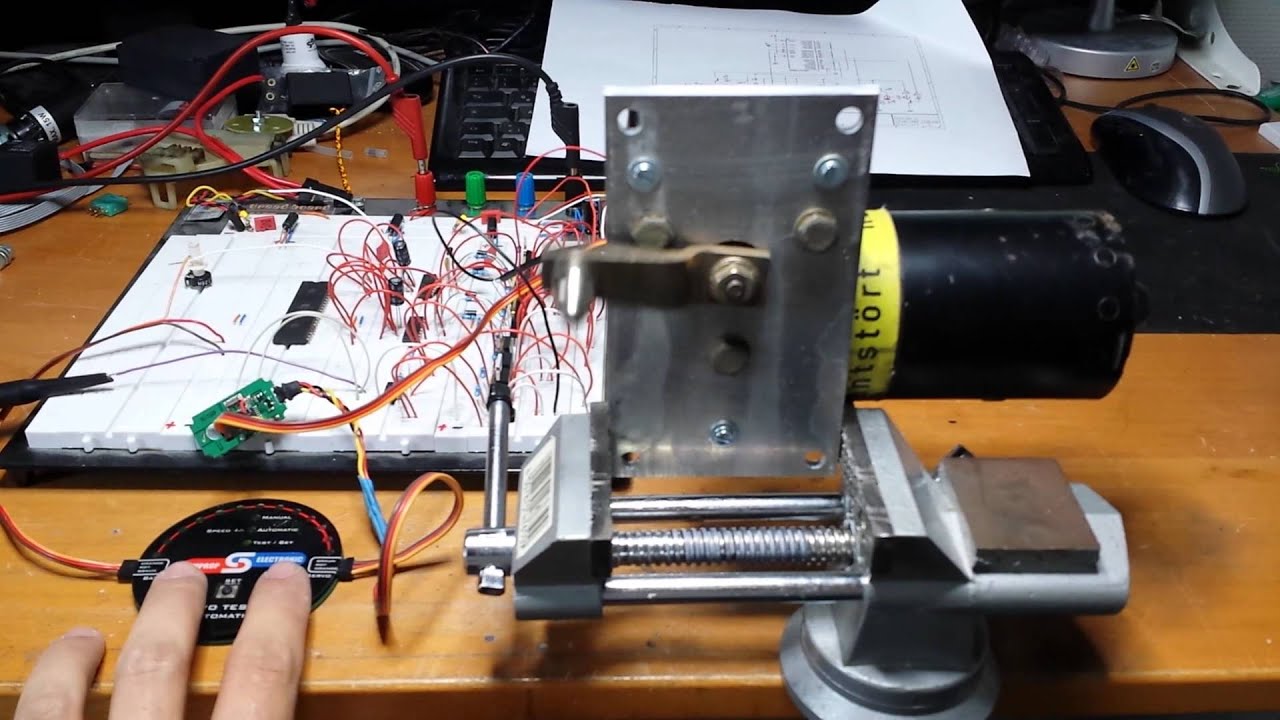
Servo Position Control with Weight (Force Sensor).Servo Motor Interfacing with 8051 Microcontroller.1ms of ON time and 17ms of OFF time in a 18ms signal.įor the shaft to be moved to 12o clock the ON time of signal must be 1.5ms and OFF time should be 16.5ms. This ratio is decoded by control system in servo and it adjusts the position based on it. This PWM in here is generated by using ARDUINO UNO.īefore Connecting Servos to Arduino, you can test your servo with the help of this Servo Motor Tester Circuit. Based on this DUTY RATION the control electronics adjust the shaft.Īs shown in figure below, for the shaft to be moved to 9o clock the TURN ON RATION must be 1/18.ie. The important thing here is the DUTY RATIO of the PWM signal. The frequency of PWM (Pulse Width Modulated) signal can vary based on type of servo motor. This data regarding position of shaft is sent through the SIGNAL pin. The position data to the control should be sent in the form of PWM signal through the Signal pin of servo motor. Simply speaking the control electronics adjust shaft position by controlling DC motor. The RED wire is connected to power, Black wire is connected to ground and YELLOW wire is connected to signal.Ī servo motor is a combination of DC motor, position control system, gears. The position of the shaft of the DC motor is adjusted by the control electronics in the servo, based on the duty ratio of the PWM signal the SIGNAL pin. A servo motor will have mainly there wires, one is for positive voltage another is for ground and last one is for position setting. Servo motors are available at different shapes and sizes. So you have to use separate power supply for the motors, either it be from some adapters (5v 2A) or from good quality 9v batteries.īefore going into detail, first we should know about Servo Motors. Connecting multiple Servo Motors with Arduino seems to be easy and but if we connect all the Servos to Arduino supply pins then they won’t work correctly because of lack of enough current to drive all the motors.
#LARGE SERVO MOTOR ARDUINO HOW TO#
Here, we are going to show you that how to control Multiple Servo Motors with Arduino. We will controlling serov using Pin 3.Using one or two Servo with Arduino is Easy but what if we want to use more than one Servo Motors?
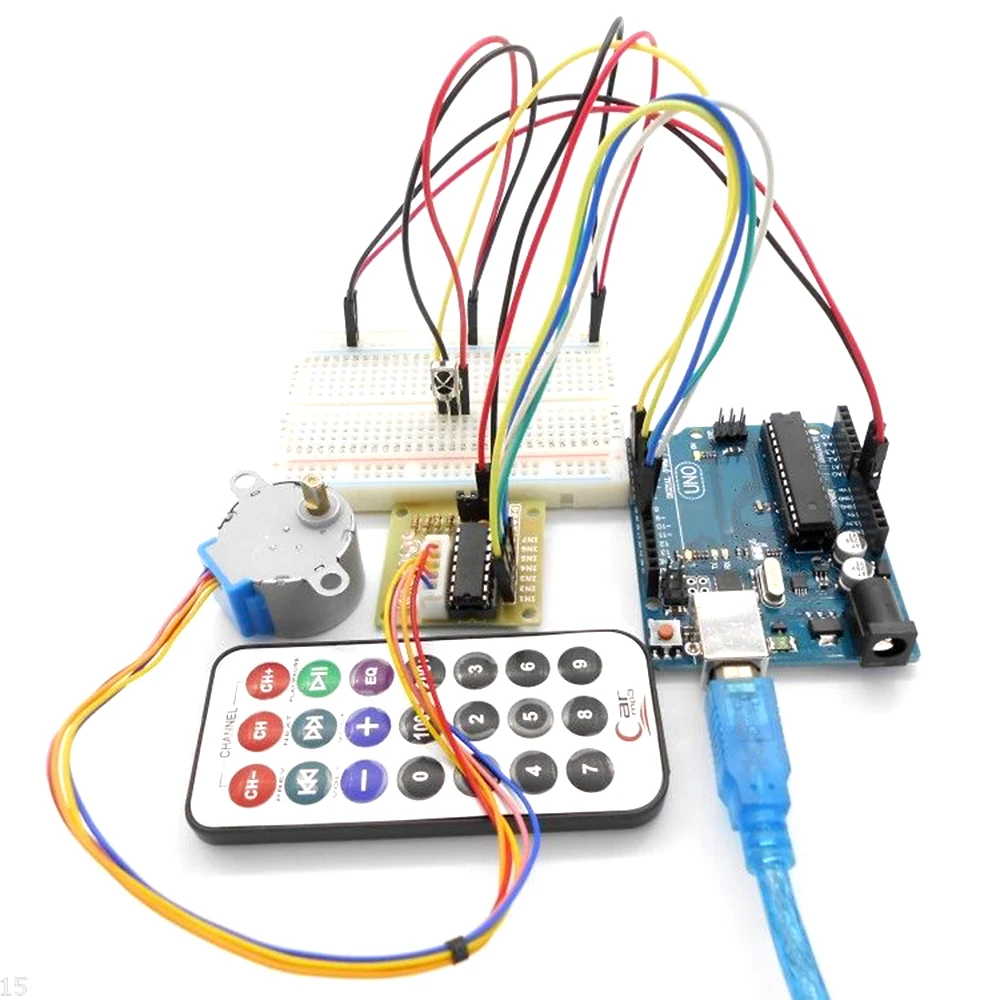
Controlling Servo using Arduino UnoĪrduino uno has 6 PWM pins: 3, 5, 6, 9, 10, and 11 which provide 8-bit PWM output with the analogWrite() function.

In this example we will attach a servo motor and set the angle of the servo to 90 degrees. Return true if this servo is attached, otherwise false Returns current pulse width in microseconds for this servo (was read_us() in first release) Returns current pulse width as an angle between 0 and 180 degrees If value is < 200 its treated as an angle, otherwise as pulse width in microseconds
#LARGE SERVO MOTOR ARDUINO FREE#
The available functions are provided in the table below:Īttach the given pin to the next free channel, sets pinMode, returns channel number or 0 if failureĪs above but also sets min and max values for writes There is a servo library which can be used to control the servo motor. The VVR (Variable voltage) should be close to 6V. Given below is the circuit diagram:Ī Servo pin has three wires (Order to be connected in evive, left to right)Ĭaution: Power evive using a 12V 2A power adapter for smooth functioning of servo motor. In the following example, I will be showing you how to control servo through channel 1. Signal pin of servo 1 is connected to digital pin 44 and servo 2 is connected to digital pin 45. Controlling Servo using evive and Arduino IDEĮvive has two dedicated servo motor outputs pins. Hence if the range of motor angular position is from 0 to 180, then minimum pulse width corresponds to 0 and maximum pulse width corresponds to 180. Minimum pulse width is the shortest time for the pulse has been HIGH and maximum pulse width is the longest time for which the pulse is HIGH. For most of the servos, a certain range of PWM correspond to the range of angle servo can rotate. The refresh interval (the minimum time to refresh servos in microseconds) is 20000, which means that the servo is refreshing at a frequency of 50Hz. Servo is controlled on the concept of PWM (Pulse Width Modulation). It consists of a suitable motor coupled to a sensor for position feedback. A servo motor is a rotary actuator that allows for precise control of angular position.
